Tager stormskridt i produktionen med 3D-print: Carmo har knækket koden
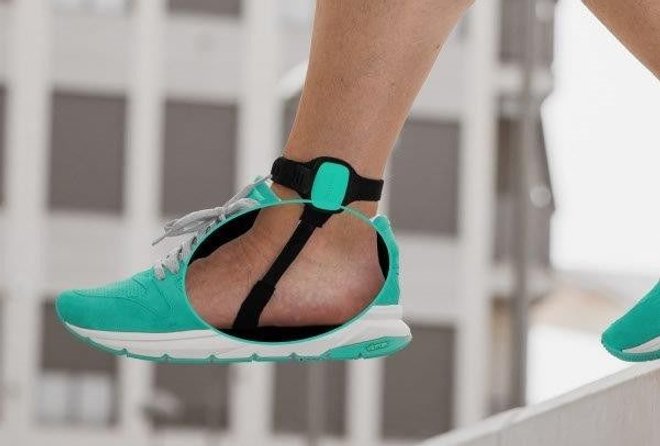
Produktionen af ni små plastdele har vist, hvad 3D-print kan i kombinationen med sprøjtestøbning. Det mener Carmo, der netop har produceret plastemner til Navigraff med en noget kortere produktionstid end sædvanligt.
- Med 3D-print og sprøjtestøbning kan vi skære måneder af udviklingstiden og holde udgifterne nede. Det betyder, at flere års udvikling, justering og test bliver skåret ned til få måneder, hvor vi løbende justerer emnerne. Vi står med en usædvanlig fleksibilitet i designfasen, der giver os et yderst hybridt set-up, som kan kombineres med industriel produktion, siger Tobias Kristensen, udviklingsingeniør hos Carmo.
Kunden - Navigraff - der udvikler og sælger sundhedsforbedrende artikler og har udviklet en teknologi, en software, til en stræksensor. Det har været en lang udviklingsproces med et mislykket forsøg på at færdiggøre produktet med en anden samarbejdspartner. Derfor var det altafgørende at finde en producent, der kunne handle hurtigt, fortæller partner i Navigraff, Frederik R. Jakobsen.
- Vi har brugt utrolig lang tid og mange ressourcer på at udvikle teknologien, så det var en stor bet, da det ikke lykkedes i første omgang, for vi kunne ikke bare finde standardkomponenter. Derfor var det helt afgørende for os, at Carmo kunne omsætte vores tanker og behov og hurtigt designede, udviklede og justerede emnerne, siger Frederik R. Jakobsen.
Carmo sprøjtestøber blandt andet komponenter til medicoindustrien, dog er behovet for kundetilpassede løsninger øget de seneste år. Derfor kigger Carmo ind i en fremtid, hvor de i langt højere grad kommer til at samarbejde med kunder under hele forløbet: Fra design over udvikling til produktion.
- Samarbejdet med Navigraff er netop den type samarbejde, vi i fremtiden kommer til at have flere af. Når vi kombinerer sprøjtestøbning og 3D-print, udnytter vi de lave omkostninger med 3D-print, og at vi med hurtige print kan finjustere produktet undervejs. Dermed giver det tætte samarbejde fra start til slut utrolig god mening, siger Tobias Kristensen.
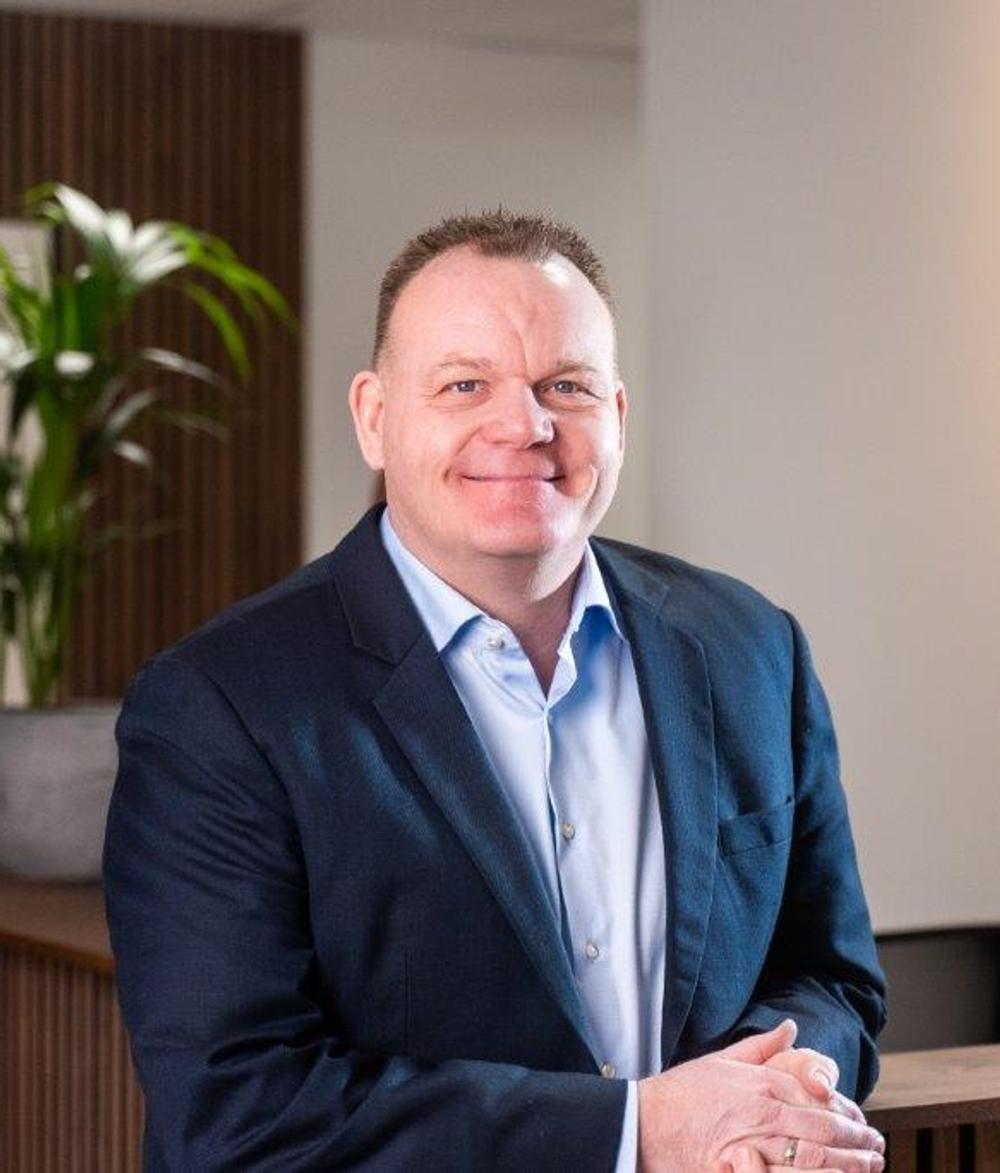
Navigraffs stræksensor går under medicinsk udstyr og er underlagt store restriktioner i forhold til materialer og produktion. Derfor har det været afgørende, at emnerne hos Carmo er lavet i et materiale, der er medicinsk godkendt.
- Vi har de seneste år taget enorme skridt inden for 3D-print, så vi også kan hjælpe producenter af medicinsk udstyr med at udvikle komponenter til medicoindustrien. Med 3D-print får vi de hurtige iterationer og den fleksibilitet, der er vigtig i den tidlige udviklingsfase. Med kombinationen af 3D-print og sprøjtestøbning kan vi producere emnerne i medico-godkendte materialer klar til test. Det er uden tvivl en game chancer indenfor udvikling og produktion til medicobranchen, fordi det reducerer time-to-market betydeligt og skærer store udgifter fra, siger Tobias Kristensen.